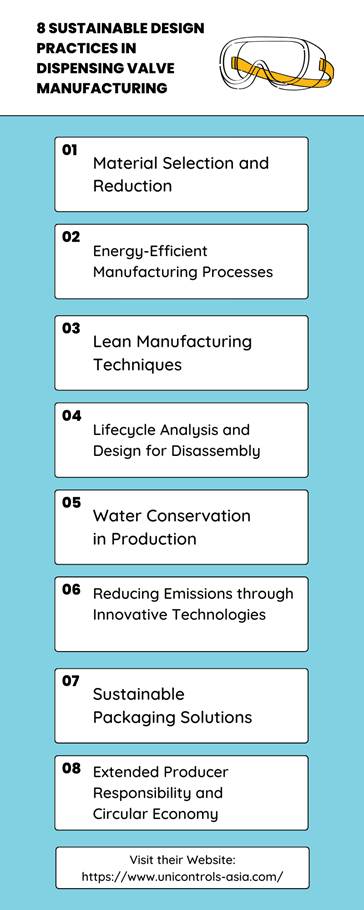
In today’s rapidly evolving industrial landscape, sustainable practices have become essential in every sector, including the manufacturing of dispensing valves. As companies seek to minimise their environmental impact, adopting sustainable design principles in dispenser valve production is no longer just a trend but a necessity. Below, we explore eight critical sustainable design practices transforming the dispensing valve industry.
1. Material Selection and Reduction
Choosing the right materials is the cornerstone of sustainable design. Dispensing valve manufacturing means selecting materials that are durable, efficient, and environmentally friendly. Manufacturers increasingly turn to recycled or biodegradable materials, reducing reliance on virgin plastics and metals. This shift not only lowers the carbon footprint of production but also helps reduce waste. Furthermore, by optimising material usage, manufacturers can create more efficient designs that require fewer resources without compromising the valve’s performance.
2. Energy-Efficient Manufacturing Processes
Sustainable manufacturing isn’t just about the end product but also the processes involved. Incorporating energy-efficient technologies into the production of dispensing valves can significantly reduce environmental impact. For instance, manufacturers are cutting down on energy consumption by adopting energy-efficient machinery, implementing smart energy management systems, and using renewable energy sources. These practices reduce greenhouse gas emissions and lead to cost savings in the long run.
3. Lean Manufacturing Techniques
Lean manufacturing is a methodology that focuses on minimising waste without sacrificing productivity. Producing dispensing valves can streamline operations, reduce excess inventory, and improve process efficiencies. By eliminating unnecessary steps and concentrating on value-added activities, manufacturers can produce high-quality dispensing valves more sustainably. Lean practices also encourage continuous improvement, ensuring sustainability is an ongoing effort rather than a one-time initiative.
4. Lifecycle Analysis and Design for Disassembly
Understanding a product’s environmental impact throughout its lifecycle is crucial for sustainable design. Lifecycle analysis (LCA) helps manufacturers assess the environmental impact of dispensing valves from raw material extraction to disposal. By incorporating LCA into the design process, manufacturers can identify opportunities to reduce environmental impact at every stage. Additionally, designing for disassembly allows for easier recycling and reuse of components, extending the product’s lifecycle and reducing waste.
5. Water Conservation in Production
Water is a critical resource in manufacturing, and its conservation is a crucial aspect of sustainable design. Dispensing valve manufacturers increasingly adopt water-saving technologies and practices to reduce their water footprint. This includes using closed-loop water systems, which recycle water within the production process, and treating wastewater to minimise contamination before discharge. By focusing on water conservation, manufacturers can contribute to preserving this vital resource while enhancing their sustainability credentials.
6. Reducing Emissions through Innovative Technologies
Innovations in technology are significantly reducing emissions in the manufacturing of dispensing valves. One such innovation is using low-emission materials and coatings, which can help minimise volatile organic compound (VOC) emissions during production. Additionally, advancements in manufacturing technologies, such as additive manufacturing (3D printing), allow for more precise production, reducing waste and emissions associated with traditional manufacturing methods. These technologies enhance the sustainability of the manufacturing process and improve the quality of the dispensing valves produced.
7. Sustainable Packaging Solutions
Sustainable design extends beyond the product itself to include packaging. Dispensing valve manufacturers are increasingly adopting eco-friendly packaging solutions, such as recyclable or biodegradable materials, to reduce environmental impact. Additionally, manufacturers can reduce transportation emissions and waste by designing packaging that uses less material or is more compact. Sustainable packaging aligns with ecological goals and meets consumer demand for eco-conscious products.
8. Extended Producer Responsibility and Circular Economy
Extended Producer Responsibility (EPR) is a policy approach that holds manufacturers accountable for the entire lifecycle of their products, including end-of-life disposal. In the dispensing valve industry, this means designing products with recyclability and reuse in mind and establishing take-back programmes for used valves. EPR encourages manufacturers to think beyond the immediate use of their products and consider how they can contribute to a circular economy where resources are reused and recycled rather than discarded.
Conclusion
Sustainable design in dispensing valve manufacturing is not just about making environmentally friendly choices. It’s about creating a more efficient, cost-effective, and responsible production process. By adopting these practices, manufacturers can significantly reduce their environmental impact while meeting the growing demand for sustainable products.
Visit Unicontrols for further details.